6 Tips to Reduce the Cost of Paper Displays
By Shenzhen Topwon Group Co.,Ltd
Mar 01, 2025
Many of the retailers and brand manufacturers we work with are under budgetary pressure. While we believe that paper displays should be viewed as an investment rather than a cost, this belief doesn’t change the reality that budgets are tight and everyone is looking to maximize returns. Here are 6 ways Topwon can reduce the cost of your next paper display stand project, culled from years of experience in the industry:
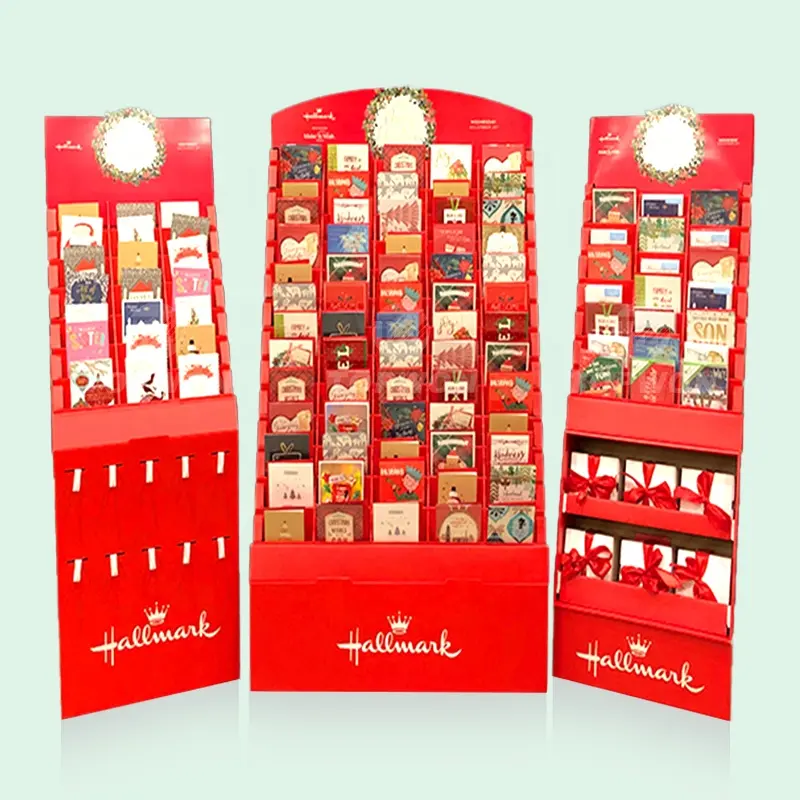
Tips 1: Plan ahead
The longer the delivery time, the more you can reduce the cost of your display stand. It’s not a matter of avoiding expedited costs, but rather delivery time affects the sourcing process because more time allows you to identify the best source. Often, if you have the time, producing paper display stands domestically is one of the best ways to save money. For many types of displays, there is a natural advantage to domestic pricing for materials and processing costs, and you can save 30%-40%. Allowing more time also allows manufacturers to optimize the production process, which can save you money.
Tips 2: Increase the quantity of a single purchase
The relationship between price and quantity is well known in the paper display industry, but the economics behind this relationship is real. Larger quantities enable manufacturers to:
- Obtain better prices for raw materials;
- Amortize tooling costs over larger quantities of equipment;
- Reduce setup time per piece of equipment;
- Create a more efficient production process .
In addition, most manufacturers are willing to accept lower margins on larger projects. All of these factors contribute to lowering the unit cost of display orders placed by customers. Therefore, it is important to consider the trade-off between lower display costs and the costs of retaining additional units for a longer period of time.
Tips 3: Choose the most appropriate materials
Discuss your material options with the paper display-stand manufacturer. If you are looking for metal display shelves, save money by using wire shelves instead of sheet metal shelves. Typically, the thicker and heavier the materials, the more expensive the display will be. To consider sheet metal shelving versus perforated sheet metal shelving, note that the perforation process represents an additional step in the manufacturing process and is therefore more expensive. Similarly, chrome finishes are more expensive than powder-coated finishes, primarily because chrome plating involves a more complex process and more environmental regulations. If you are interested in wood displays, wood composites, such as MDF (medium-density fiberboard, are often cheaper than solid wood materials.
There is a lot to know about materials and it can be difficult to be an expert in all material categories. You can have a paper display stand company explain the cost and performance differences between various material options. Fortunately you can choose the right material to make the display stand according to your budget and design.
Tips 4: Consider the material consumption
Material consumption is a very important cost factor. Often, material yield comes into play when considering materials that come in the form of sheets. During the design phase of a paper display project, try to specify dimensions for optimal material consumption. In the United States and worldwide, most standard paper sizes are 4′ x 8′. So, for each component of the display, try to figure out the size that will yield the most pieces from a 4′ x 8′ worksheet. Another way to look at it is how do you minimize paper waste?
For example, if your floor fixtures have shelves, consider making them 23.75″ x 11.75″ instead of 26″ x 13″. In the first case, you’ll get 16 shelves per sheet, while in the second case, you’ll only get 9 shelves per sheet. The net effect of this yield difference is that your shelves will be over 75% more expensive in the second case due to suboptimal quality.
Tips 5: Choose a display shelf with a disassembled design
As opposed to a fully welded or fully assembled design, a modular design can help reduce your display costs. The main advantage of a modular design is the reduction of transportation costs, which includes not only ocean freight costs when manufacturing paper displays abroad, but also domestic transportation costs. Clever modular designs also allow parts to nest in smaller spaces. For example, if your display has multiple baskets, the fronts and sides of the baskets may be angled slightly to allow the baskets to nest. The right combo design can often result in a box that is half the size of a fully welded or fully assembled box. In addition to reducing shipping costs, combination displays can also reduce the cost of damage that may occur during transportation. Unless shipped on pallets, many fully assembled units are susceptible to damage, which can result in higher shipping costs relative to parcel shipments.
Tips 6: Use inexpensive ocean transportation
That’s right, it’s the use of a different shipping method that will save money on the overall project side by side. Plan your purchases well in advance. For example, if a retail store is going to do a promotion related to women’s theme on March 8, then plan months in advance and calculate the time for design, production, transportation, and assembly. This is also just the right amount of time to calculate the cost through the long sea transportation.
In short, saving costs, does not mean cutting corners, but to go in all aspects of the comprehensive consideration, in the case of ensuring the overall quality of the paper display rack, to reduce the cost down.
Trusted by These Featured Clients