Nine tips for solve the printing colour difference of cardboard displays
By Shenzhen Topwon Group Co.,Ltd
Aug 14, 2024
In the daily printing and production process of cardboard displays, how to maintain the consistency of printing colour has always been a problem for printing producers. Many manufacturers have also experienced problems, customer complaints and even returns due to colour differences in cardboard display racks, resulting in serious quality incidents. Nine tips for solve the printing colour difference of cardboard displays
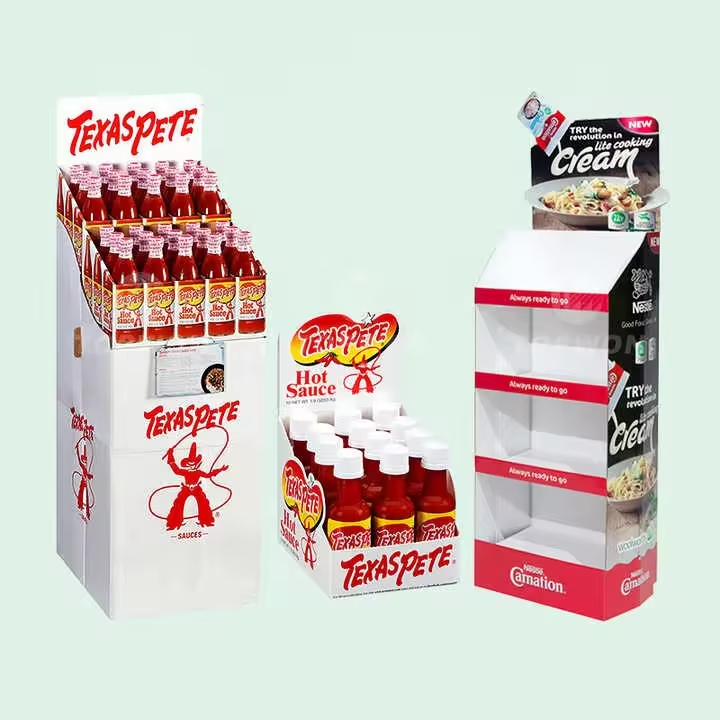
- making suitable printing plates
- colour samples and colour cards
- control ink
- control speed
- control from the printing pressure
- Ensure anilox rollers are clean
- Printing standard light sources
- Ensure ink printing quality
- Knowing the pattern of colour change after drying of special colours
Making the right printing plate
It is not uncommon for us to encounter a situation where the colour of the product printed during a sample run is far from the colour of the sample provided by the customer. This situation depends mainly on the network density, size and sample on the printing plate. Due to the different web densities and sizes, the following steps are recommended for improvement.
Firstly, measure the number of lines added to the sample with a special netting ruler to make sure that the number of lines added to the printing plate and the number of lines added to the sample are the same.
Secondly, through a magnifying glass to observe the various colours on the printing plate dot size and the sample corresponding to the size of the colour of the network is consistent, if not consistent, it needs to be adjusted to the same or similar size. It should be noted that, as the printing point will increase, plate making set the dot size slightly smaller than the sample on the dot.
Colour samples and colour cards
The source of printed colours comes from the customer’s colour samples. If the colour samples are not accurate, the production unit cannot guarantee that the printed colours will be the same as those of the customer. After taking the colour samples from the customer, the manufacturer should consult with the customer to determine the printing colour and formulate the printing colour.
After formulating the colour samples, the manufacturer must keep them strictly. Colour samples and colour cards are best for three months. Replace them once to achieve permanent hue, brightness and saturation. This facilitates consistency between the customer and the colour manufacturer, and the manufacturer has access to accurate print colour requirements and can access the colour range for reasonable control.
Controlling the ink
During the actual printing process, the two characteristics of the ink, viscosity and viscosity PH, should be controlled. Proofing to confirm the viscosity and PH value of the ink, customer confirmation and then production installation of proofing ink viscosity and PH check the value and fineness of the ink; on the machine before the stirring of the ink and ink pumps installed on the ink supply system; if the ink is not stirred for a long time, the resin in the ink will be precipitated, and once the precipitation, the colour of the ink will become darker. Therefore, the addition of an ink pump helps to control the viscosity of the ink. The key control of the ink is in the data logging, using the data values to control the colour of the ink and using the ink pumps to control the viscosity of the ink, allowing the resin in the ink to flow, which can improve the flow of the ink. This is one of the conditions necessary to maintain consistent colour.
Controlling speed
The speed of the press is a very critical point. For example, there will be a big difference between printing colours at 70 sheets/minute and 180 sheets/minute. As the rubber rollers in the printing press are high, the speed and equipment vibration vary; equipment vibration brings the amount of ink between the rubber rollers. When the ink volume is larger, the colour will become darker. Therefore, the gap between the printing adjustment machine and the normal production speed should not be too large. To maintain the printing speed during the production process, it is necessary to maintain an even production speed. If the printing speed is not even, there will be some dark and some light in a batch of orders. In factories, the incidence of this situation is still relatively high, so some well-known companies According to the characteristics of the equipment to develop appropriate printing test machine and production speed requirements.
Controlling print pressure
In order to achieve colour consistency in the same batch of orders, printing pressure is also an important factor to be controlled. It directly affects the change of printing colour. The printing of this machine
Printing pressure includes two aspects, one is the contact pressure between the web roller and printing, and the other is the contact pressure between printing and cardboard. Therefore, in order to control the consistency of printing colour, it is necessary to
Maintain a stable and uniform printing pressure. The effect of printing pressure on colour is not the main reason. Printing pressure indirectly affects the characteristics of the printed colour, and should be lighter when controlling the printing pressure.
Ensure clean anilox rollers
In addition to the above, make sure that the anilox rollers in each printing unit are cleaned before printing. This is because if the anilox roller’s mesh is clogged, it will affect the uniformity of ink transfer, and the printed pictures and text will not be as good as they could be.
and the printed pictures and text will have uneven colours. Cleaning of the anilox roller is very important. For example, if the mesh is clogged, the amount of ink on the ink will be directly reduced, the printed colours will be lighter, and the saturation of the colours of the printed brushes will not be high enough, so it is important to clean the anilox rollers of the printing machine regularly.
Printing Standard Light Sources
Some manufacturers of cardboard frames do not use a standard light source for printing, which poses a risk to the control of colour consistency of the printed product. The colour of the product seen under the illuminated light source during the night shift is very different from the colour of the product seen under the sunlight during the day shift, and therefore can easily lead to differences in printed colours. Therefore, it is recommended that the printing workshop must use the printing standard light source for lighting, if necessary, equipped with a standard light source box.
Ensure ink printing quality
The quality of the ink itself and the quality of printing machines and equipment will directly or indirectly affect the quality of printing, no matter how well the other work done in front of it, it is difficult to achieve the ideal state, so we must control the relevant quality.
Mastery of special colours after drying the law of discolouration
Printing colours are ever-changing. Some colours are very close to the sample colour at the beginning of printing, but after drying, they are very different from the sample colour, especially the dark colours made of inks such as shooting blue.
When printing with blue ink, the red situation after drying is very obvious, and attention must be paid when printing. In addition, gold and silver and other metal inks, due to the ink composition, its monochrome or special deployment of the
colour inks also change after drying. At the same time, the colour effect of the printed product is greatly affected by the observation angle Therefore, when printing with this ink, you should know in advance the customer’s observation environment
Under the sunlight or light, try to keep the consistency.
The printing process is a dynamic equilibrium process, each stoppage will cause colour difference. Therefore, the uniformity of printing colour has become an important indicator of printing quality.
Many tips are printing process hope that the above experience can help industry peers to better control the printing colour and produce more personal and attractive cardboard displays to make the retail brand more vivid.
Trusted by These Featured Clients